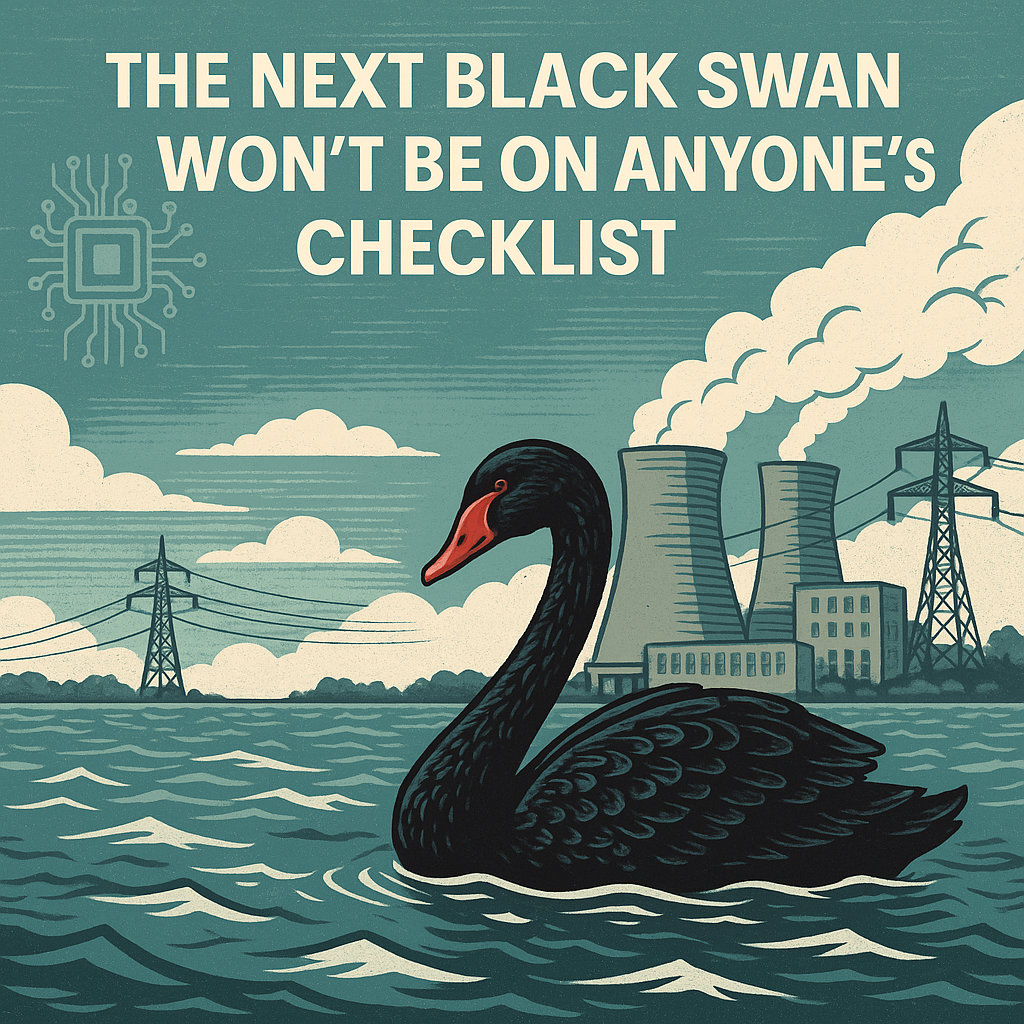
Why Trust, Context, and Meaning Are the Foundation of Resilient Operations
The flood in Abu Dhabi was a Black Swan — once.
Now everyone’s digging drains, installing water sensors, and putting “flood” on the risk register.
Just like they’ve done with cyberattacks.
And system faults.
And random hardware failures.
But what about the next Black Swan?
The real kind. The one that’s not in your SOP, doesn’t log to your historian, and doesn’t show up in your digital twin dashboard until it’s too late.
The Problem with AI Platforms in the Real World
Everyone wants AI-powered platforms today. Energy. Water. Industry. Cities.
Billions go into centralized dashboards, unified data lakes, and top-down optimization.
But as Taleb said:
“Optimization makes you fragile. The most robust systems are those that sacrifice efficiency for redundancy.”
If your AI lives in the cloud, and your edge is dumb, what happens when the link breaks?
Or when the sensor lies?
Or when the event simply wasn’t part of the model’s training?
That’s not theory — that’s the real world.
A Different Approach: Meaning-Driven Predictive Maintenance
We’re building something different. Not just AI, but interpretable intelligence at the edge — grounded in the physical reality of the plant.
Here’s what makes it work:
- “Meaning Tags” that embed context into every signal: what it is, where it comes from, and what it affects — all in human-readable form
- Correlation engines that connect control system logs with operator notes, manuals, weather conditions, and equipment datasheets
- Knowledge containers — modules tailored to specific assets that actually understand what a trip, stall, or vibration means for that turbine
- CEM evolution — built on what we’ve deployed already, not theoretical prototypes
- Edge-first design — because power plants don’t run in the cloud
This isn’t just about prediction. It’s about contextual awareness.
The ability to ask, in real language:
“What happened in my plant in the last 24 hours?”
And get an answer that makes sense.
Resilience Over Optimization
Preventive maintenance replaces parts too early.
Reactive maintenance replaces them too late.
Our approach uses 20 years of operational data — from real power plants — to understand what really matters, and when.
It’s not just statistics. It’s structure.
And that structure comes from putting meaning first.
Because you can’t prepare for Black Swans by optimizing harder.
You prepare by making your systems explainable, interpretable, and built to survive what wasn’t expected.
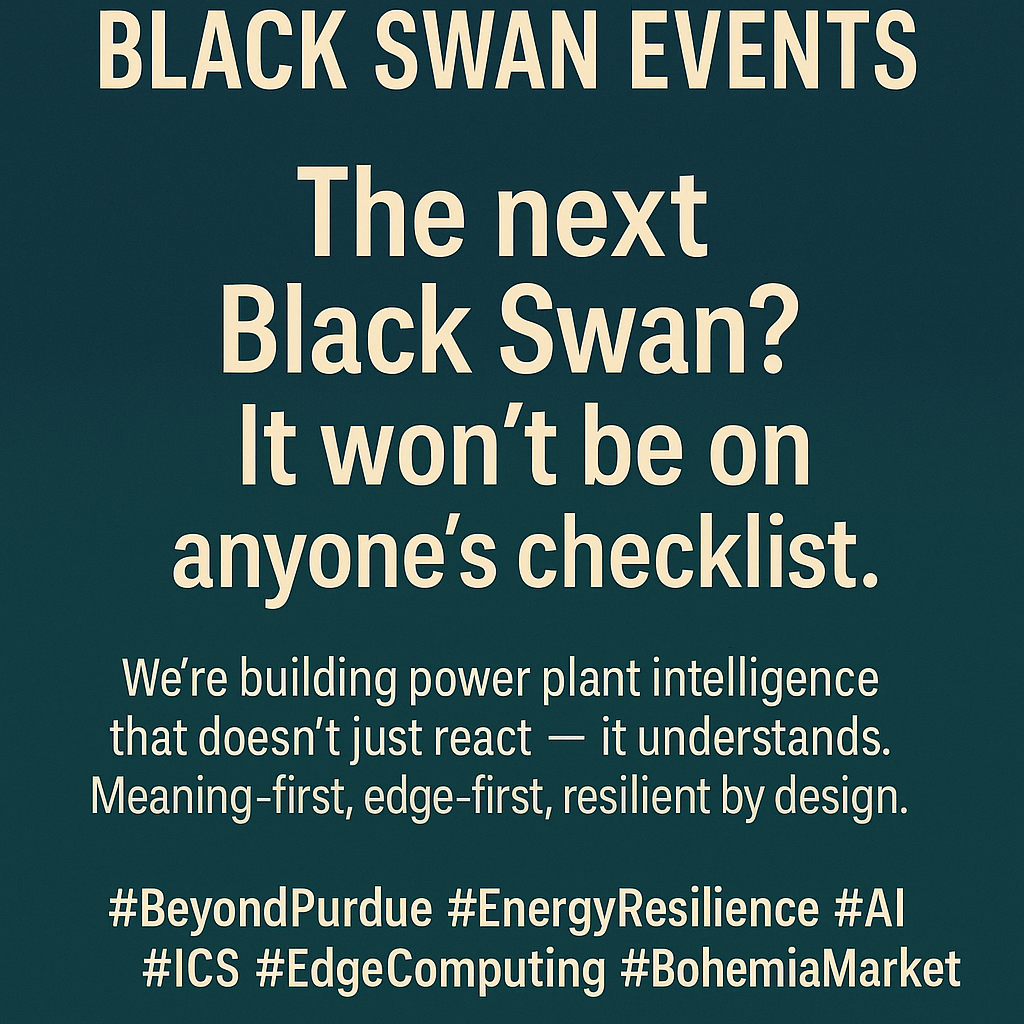
Final Thought
The question isn’t whether your platform can deliver a forecast.
It’s whether it will still work when the world breaks the forecast.
And when that happens, what will your plant know?
What will your people see?
That’s where resilience lives.
Leave a Reply